Kiinassa kalsinoidun koksin pääasiallinen käyttöalue on elektrolyyttinen alumiiniteollisuus, jonka osuus kalsinoidun koksin kokonaismäärästä on yli 65 %. Seuraavaksi tulevat hiili, teollisuuspii ja muut sulatusteollisuudenalat. Kalsinoitua koksia käytetään polttoaineena pääasiassa sementti-, energiantuotanto-, lasi- ja muilla teollisuudenaloilla, joiden osuus siitä on pieni.
Tällä hetkellä kalsinoidun koksin kotimainen tarjonta ja kysyntä ovat pohjimmiltaan samat. Vähärikkisen ja korkealaatuisen maaöljykoksin viennin suuren määrän vuoksi kalsinoidun koksin kokonaistarjonta kotimaassa on kuitenkin riittämätöntä, ja keskirikkistä ja runsasrikkistä kalsinoitua koksia on edelleen tuotava täydennykseksi.
Viime vuosina Kiinan kalsinoidun koksin tuotanto kasvaa, kun koksaamoja on rakennettu runsaasti.
Rikkipitoisuudesta riippuen se voidaan jakaa runsasrikkiseen koksiin (rikkipitoisuus yli 3 %) ja vähärikkiseen koksiin (rikkipitoisuus alle 3 %).
Vähärikkistä koksia voidaan käyttää anodisena tahnana ja esipaistettuna anodina alumiinitehtaassa sekä grafiittielektrodina terästehtaassa.
Korkealaatuista vähärikkistä koksia (rikkipitoisuus alle 0,5 %) voidaan käyttää grafiittielektrodin ja hiiletysaineen valmistukseen.
Esipaistettujen anodien valmistuksessa käytetään yleisesti yleislaatuista vähärikkistä koksia (rikkipitoisuus alle 1,5 %).
Heikkolaatuista maaöljykoksia käytetään pääasiassa teollisen piin sulatuksessa ja anodisen tahnan tuotannossa.
Runsasrikkistä koksia käytetään yleisesti polttoaineena sementtitehtaissa ja voimalaitoksissa.
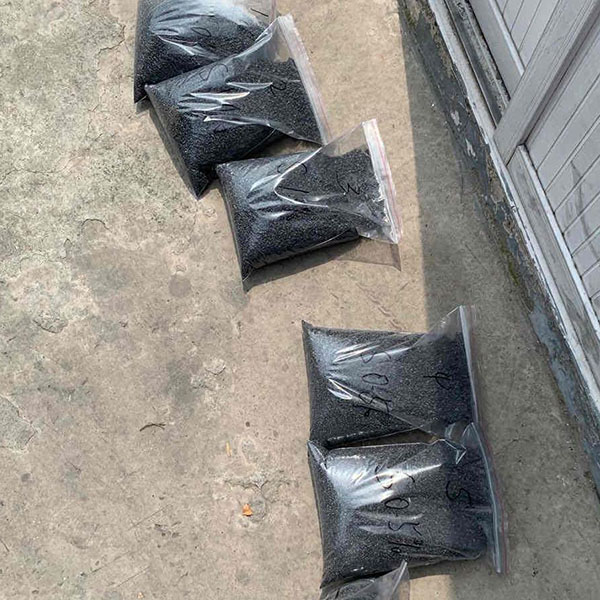
Jatkuva ja tarkka näytteenotto ja testaus on olennainen osa tuotantoprosessiamme.
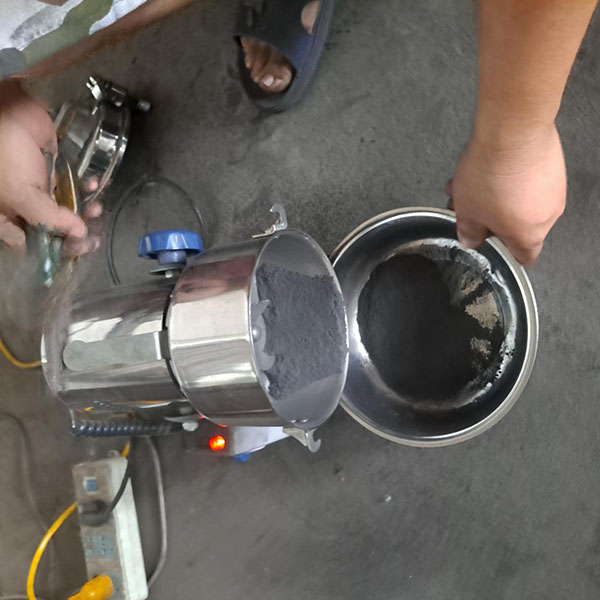
Korkean rikkipitoisuuden omaava koksi voi aiheuttaa kaasun turvotusta grafitisaation aikana, mikä johtaa halkeamiin hiilituotteissa.
Korkea tuhkapitoisuus estää rakenteen kiteytymistä ja vaikuttaa hiilituotteiden suorituskykyyn
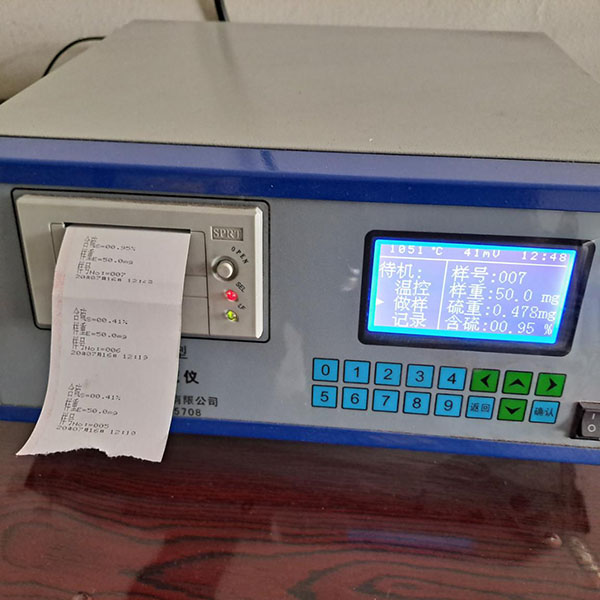
Jokainen vaihe testataan huolellisesti, haluamme tehdä juuri havaitsemisdatan.
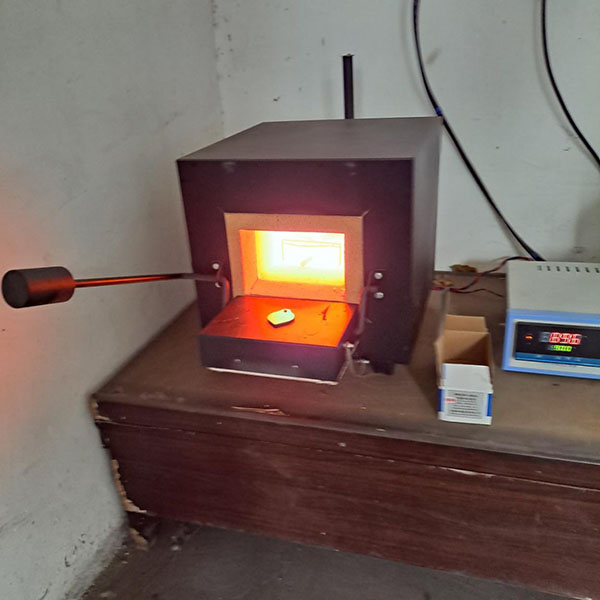
Laatujärjestelmämme mukaisesti jokainen paketti punnitaan vähintään kolme kertaa ristiriitaisuuksien välttämiseksi.
Ilman vihreää kalsinoitua koksia resistiivisyys on erittäin korkea, lähellä eristettä, kalsinoinnin jälkeen resistiivisyys laski jyrkästi, kääntäen verrannollinen maaöljykoksin resistiivisyyteen ja kalsinointilämpötilaan, 1300 ℃:n jälkeen kalsinoidun maaöljykoksin resistiivisyys laski noin 500 μm Ω m:iin.
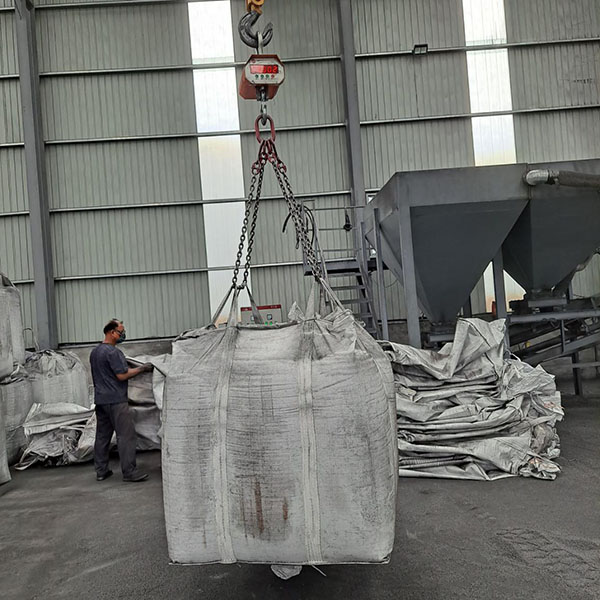
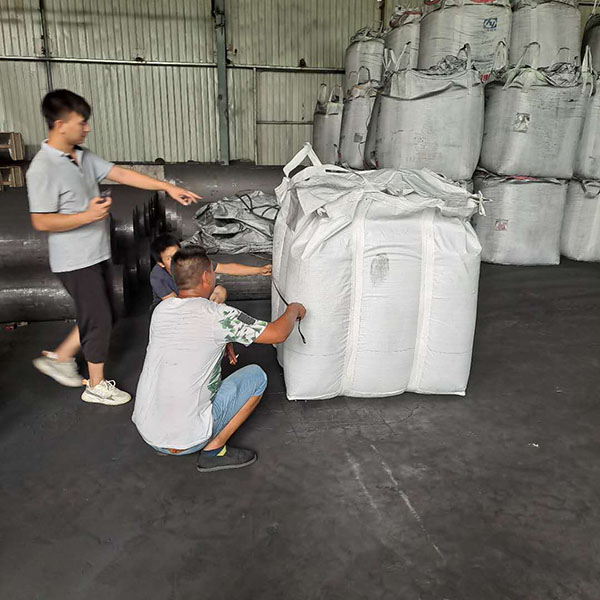
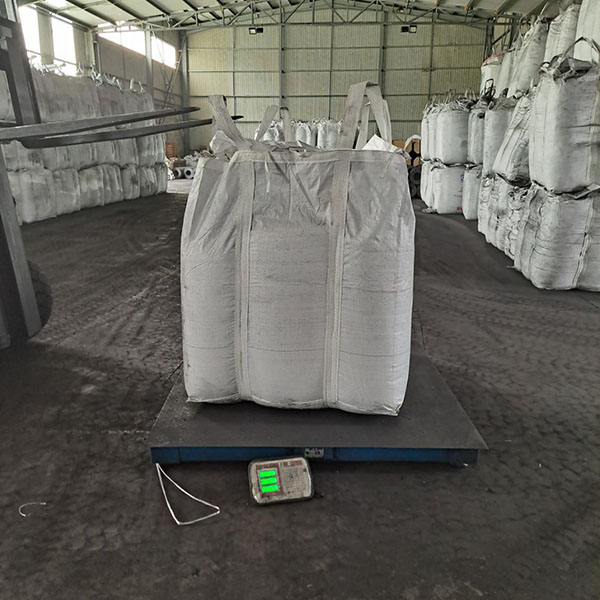
Julkaisun aika: 20.12.2024